FIMI-VIGANO' 1500x2mm CTL Line (Used) #4290
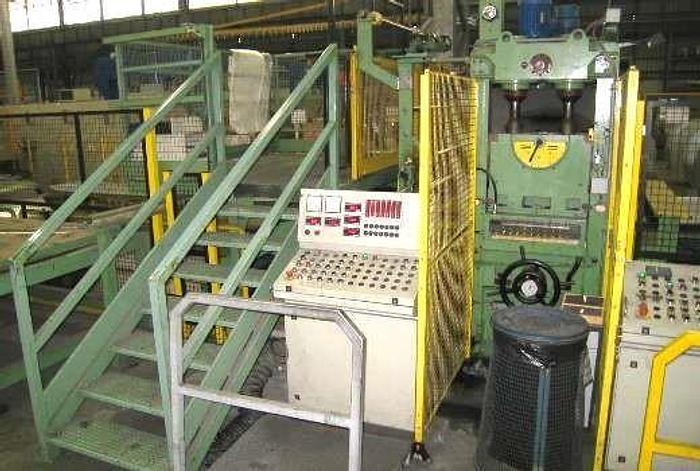
FIMI-VIGANO' 1500x2mm CTL Line (Used) #4290
Description
Roll Feeder Type Line
of 1999
0-60m / minute
for:
- aluminium
- cold rolled / electro-galvanized & galvanized / prepainted / stainless steel
^
Tensile strength max.: 500 N/mm2
Yield strength max.: 380 N/mm2
Coil width: 250<>1550mm
Material thickness: .35<>2.0mm
Coil weight: 20ton max.
Coil ID: 508mm > 610mm* ( * using 'overtiles' )
Coil OD: 800mm > 1800mm
Sheet lengths: 400mm to max. 5000mm
Sheet stack weight: max. 3ton
Specific stack load: max. 1500kg/m
Stack height including pallet*: max. 500mm
(Stacking on wooden pallet)
Length accuracy:
-- max ± .25mm at constant speed, for sheets up to 2000 mm
-- for every additional 1000mm ± .10mm must be added
A
LINE GENERAL FEATURES
Line direction:
Right to Left
Line reference:
Center
Passline height:
1100mm
Feed speed:
15m / minute
Stacker / start-stop function mode:
the line must be stopped at each batch-unloading.
ELECTRICAL POWER SUPPLY
LINE VOLTAGES
Three-phase voltage 380 V 60 Hz
Auxiliary voltage 220 V 60 Hz
Voltage of electrovalves 110 V
Hydraulic power pack
Operating pressure (nominal) 100 bar
Pneumatics
Operating pressure (nominal) 6 bar
Ambient temperature min. 5 °C / max. 40°C
B
EQUIPMENT DESCRIPTION
B01) ENTRY COIL CAR
- Coil car "levers-pantograph type", overfloor level, movable by hydraulic motor
- Hydr. “V”-shaped saddle covered with anti-scratch material, to support coil
- Car capacity: 20ton
B02) UNCOILER
- Movable with regard to centre line axes, ±100mm mm -- to hold the material centered
- D.C. motor driven.
- With pneumatic stand-by brake
- Uncoiling: from top side
OVERHUNG MANDREL ^
- ø 508mm, table approx. 1650 mm
- ø 610mm obtained with additional segments
- "Nose" for third support (> capacity 20 Ton) to avoid deflection of the mandrel
PRESSURE ARM ^
- Up/down movement by hydraulic cylinder
- Roll rotation: by hydraulic motor
- Roll ø 180mm, roll length 500mm; with passage for central strap.
3rd-SUPPORT for UNCOILER ^
- Hydraulic cylinder to move the frame in position, or outside the limit of the uncoiler
- Up/down movement by an hydraulic internal cylinder
B03) COIL OPENING TABLE
- Opening: from top side
- Table with fixed opening tooth
- Lifting/extension movements powered by means of hydraulic cylinders
B04) FEEDING PINCH ROLLS
- 2 rubberized rolls
- introduce the material to leveler
- lower roll rotation: by hydraulic motor
- upper idle roll vertical movement by hydraulic cylinders
B05) LEVELER
- 6-Hi type
- Roll cassette: with19 work rolls, diameter 45mm
- Upper leveling rolls: 9
- Lower leveling rolls: 10
- Rotations of rolls by D.C. motor, with stand-by brake
- Lower back-up roll parabola adjustment by 7 hydraulic cylinders
- Localized correction digital readout (on video)
- Penetration-indication digital readout (on video)
B06) PLASTIC FILM DISPENSER
- to apply a protection film on the upper surface of material
B07) Entry/Exit Saddles with vulcanized rollers for the material loop; two overpass-tables, movable laterally by action of pneumatic cylinders
- The first ^ supports the material during introduction phase, the second (on the floor) supports the material at exit to avoid possible scratches and the noise. -- The loop is complete with a series of photo-cells for min. and max loop, to control the material and prevent damages to the material and to the machines. On the exit saddle, there are some vertical rolls to contain and guide the material for perfect squareness
B08) ROLL FEEDER
- 2 rolls (D.C. motor driven) to feed material to the static Shear
- Tacho-meter Wheel to measure the length of strip
B09) GUILLOTINE SHEAR
- with manual blade clearance adjustment
B10) CONVEYING SYSTEM
Exit Conveyor after Shear
- Belt rotation by A.C. VVVF electric motor
- Deflector Belt Conveyor to separate scrap from 1st-choice sheets
- Up / down movement by hydraulic cylinder
Scrap car
- Max. sheet length: 1000mm
- Manual sideways extraction
Belt Conveyors
- To deliver 1st-choice sheets to Stacker -- 1 inclined overpassing belt conveyor
- Belt rotation by A.C. VVVF electric motor
Under the conveyor there is a Pallet introduction system (laterally movable, to deposit the new pallet) provided with a pusher, to load and introduce the pallet on the chain-platform under stacker when the line operator moves off-line a finished sheet pack
Air Ventilator for “air cushion” (next), to support sheets during stacking phase
B11) STACKER - AIR TYPE
- Single box type (1 x 4500mm)
- Pallet length 4500mm; it can be loaded by the specific Device (see B10^)
B11.1) STACKING PLATFORM
- Static type, secured to foundation
- Useful length 4500mm
- Lifting movement by hydraulic cylinders
- Provided with motorized chain-way table and Weight Load Cells, to achieve weight: 5000kg
- Chain rotation by A.C. VVVF electric motor
- Stack off-loading: along line axis
B11.2) EXIT CHAIN-WAY
- Static type, secured to foundation
- Chain rotation by A.C. VVVF electric motor
B11.3) "SIGNODE" POWERED STRAP FEEDER, MOD. PSF-2-RSI - STATIC
- Suitable for ¾” steel straps --- to bundle the finished pack of sheets
- Semi-automatic system: just one operator is required to operate it
B11.4) EXIT CHAIN-WAY
- Static type, secured to foundation
- Chains rotation by A.C. VVVF electric motor
- Unloading: by fork lift* (* fork lift not included)
B12) HYDRAULICS & PNEUMATICS
- Hydraulic central unit (location at max. 6m from main line axis)
- Oil cooling air-forced heat exchanger
- Hydraulic electro-valves -- of single stand grouping design, on board of each machine
- Spilling oil collecting tray, installed underneath each hydraulic manifold
B13) PNEUMATIC EQUIPMENT ^ to FIMI standard
- On-board-mounted pneumatic valves for each machine
B14) ELECTRICALS & ELECTRONICS
- Motors and sensors onboard-installed for each machine.
- Air ventilated, IP23 Electric cubicles (air conditioning not included)
-- Digital HMI on operator control desk (level 1)
B15) PROTECTION FENCING and Safety Barriers by photocells
- Material guards on machines and equipment-perimeter around the line
- Photocells Security for scrap car, pallet introduction system and exit chain-ways
- Automatic fence-barrier to entry side of coil car-elevator
-
Specifications
Manufacturer | FIMI-VIGANO' |
Model | 1500x2mm CTL Line (Used) #4290 |
Condition | Used |
Stock Number | 1704165 |