F&P Ø120mm Tube Laser (New) #3486
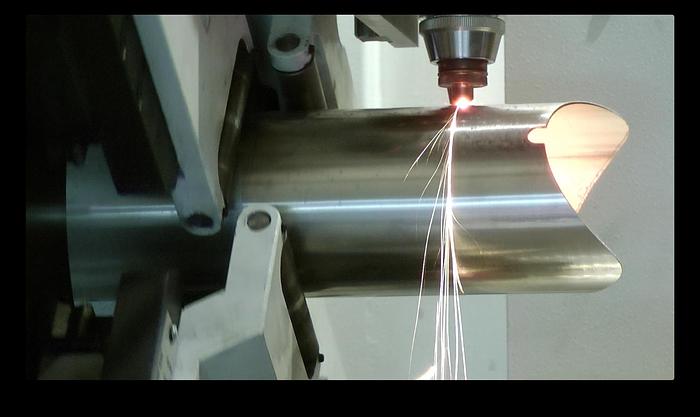
F&P Ø120mm Tube Laser (New) #3486
Description
Ø120mm Tube Laser (generally available ex-stock or, with short delivery) -- Our Fiber Laser Model for tube diameters from 20mm to 120mm / Main Data: --Materials: steel (carbon, stainless), aluminium, other alloys --Part loading system: standard length 6000mm; different lengths on request --Max tube weight: 35 kg/m --Max bundle weight: standard 4000 kg, different weights on request --Part unloading system: standard length 3000mm, different lengths on request --Cutting head brand: Procon --Capacitance sensor: Precitec --Laser source: N’Light --Tilt cutting head: +/- 43° both axes -- Connection for tele-assistance included -- Details: Part loading system ^ (we can propose different types accordingly to customer’s needs) Feeding system for a single tube Cutting head Unloading station (Possibility to add collection bin) Scrap evacuation conveyor Standard capacity of the System: • Spindle capacity from ø20mm round, 15×15 square. • Maximum capacity Ø120mm round • Capacity on rectangles with measures inscribed in a circle ø120mm • 1.2Kw Nlight source (other Type on request) • Maximum Length loaded 6m (may be different on request) • Maximum Length unloaded 3m (may be different on request) • Rubber unloader-belt (optional) • Possibility to remove unloading sections and to combine crates and baskets CM Type Loader • Capacity: 6 meters in length and 4000 Kg maximum weight • Ability to load individual tube manually, in opposite position to the side-loader • Lower holders to support it^ during cutting and unloading operations • Length control stopper after load Controlled axes • Spindle rotation (Front, Rear) • Spindle Feed (Front, Rear) • Head movement (X, Y) • cutting focal (inside the head) • Pipe support holders (on: loading, unloading) • Arms for tube storage (on loader) Fixing the parts on spindle is the only mechanical adjustment required on the machine - Self centering spindle with clamp stroke: 90mm - Pressure on tube, that can be set up with multiples of 60 kg or 170 kg - Hydraulic opening of clamps - Opening distance among the 4 clamps synchronized, individual set-up (ex.: for rectangular tubes) - Synchrony of both spindle during working, back mobile spindle Cooling systems • Double chiller system with separate cooling system for the source and head, with different temperature set point. • cooling system compressed air nozzle • separate circuits for cooling and heads laser source Smoke extraction Suction system with 5000 m2 capacity, with purification filters and dust separation. Automatically operated during cut Head MODEL: 2D - capacitance sensor brand: Precitec - noozle cooling by air - head cooling by liquid - anti-collision system - glass quick change system - noozle can be screwed - motorized focus - movement of Y axis with algorithm, following the profile of the tube with capacitance sensor - movement of Y axis commanded by software, CAD CAM • Head with capacity up to 5KW, oversized • Transport fiber to laser 100µm • Interchangeable nozzle, interchangeable protective glass • Prepared for the use of GAS to support the cut: Nitrogen, Oxygen, clean compressed air (requires purifier / compressor apart from the group, not included) Unloader (for 2d and 3D types) • Moving shuttle system to rubber conveyor belt (rubber conveyor optional) • Unloading system L= 3000mm with 4-5 different unloading station Scrap unloading on the scrap conveyor Separation of smaller scraps than 200mm Software for the design and definition of the tubes to process: Modeling • 3D modeling of tubes and bars of any section. • Library of predefined sections (circular, rectangular, etc). • Library of extruded bars (international code). • Possibility of definition of the sections with parametric macros. • Library of predefined shapes for the holes. • Ability to define parametric macros for the holes. • Possibility to define holes of any shape. • Automatic 3D nesting with joint of the pipe ends. • Calculation of the minimum and maximum material size, also on pipes imported from CAD. • Import 3D models via STEP and IGES formats. • Automatic recognition of the pipe sections during CAD import and possibility of modifying them (addition of holes, machining, etc.). Production orders and materials inventory management • Preparation and management of work orders in a "desktop" based on the Windows® concepts. • Management of the distinct processing. • Automatic Section Control, thickness and material relating to the inserted pieces Nesting of pipes • Run the nesting of more pieces of more bars. • Optimize the number of bars to be used to cut the number of parts required. • Search for the best format among the different lengths of bars available. • Tubes engages with the cut ends in non-orthogonal way, in order to save material. • It allows you to enable and disable the rotation constraints of the tubes around their axis in function of their section. • automatically checks the distance between the pieces. • automatically it manages the common cut • It works in batch mode , without operator intervention . Programming • Associates the technological attributes (connections, micro-joints, etc.) And the cutting parameters to the profiles to be cut. • It executes the sequence of automatic or interactive cut. • It generates ISO codes via a post-processor specific. • The programming of tube cutting is implemented in a 3D environment that allows the complete modeling of the machine, with a total consideration of its kinematics (speed, acceleration, singular points), with no limit on the number of axes of the machine or of the robot. Main functions • automatic creation of cutting profiles and connections, with the management of the head orientation for beveled cutting. • interactive or automatic creation of paths, supported by a powerful route optimization algorithm of moves collision calculation. • Creation and validation of the cutting program thanks to a realistic simulation and automatic control functions with visual indication of the anomalies. • Generation of ISO programs using a specific post-processor. Factory document • Release of a specific document factory for the tube cutting technology that includes all information related to cutting programs and the placement of the pieces on the bars. CN software on machine • Dedicated system with G-code interpreter real time handling and assistance • GUI on Windows XP Embedded system, with management of all machine functions • Local Area Connection to be able to load programs to be executed • USB connection for transferring programs • 17 "display dedicated to working • Display 32 "dedicated to the cutting vision • Remote access and screen sharing system Components • Micro switch, inductive sensors Balluff, Datasensor • Safety barriers: Datasensor • Brush less motors and motion control: ESA • Contractors, components in electric cabinet: Siemens / Schneider • Electrical component follow ULCA norm • Reducers: Neugart (axes control), Motovario (handling) • Pneumatics: Metalwork • Proportional valve: Diwal • Capacitive sensor head: Precitec • Head and optical paco: Procon • Laser source: Rofin/ IPG • Chiller: Eurocold • 32 "display to follow the processing inside the machine during the working phases -- Click here for some videos: > https://youtu.be/qt-gdaST_6E > https://youtu.be/zawEEPaDARE > https://youtu.be/RCH2_Zp12vw > https://youtu.be/Um9AdYrGP38 > https://youtu.be/tEqcRplWplo > https://youtu.be/LbE5qnz0tGg -- "A technology that revolutionises the design, manufacture and assembly of tubular products."
Specifications
Manufacturer | F&P |
Model | Ø120mm Tube Laser (New) #3486 |
Condition | New |